Electric welding machines operate on the principle of converting electrical energy into heat. This heat is then used to melt and fuse metals together. The fundamental components of an electric welding machine include:
Power Source: The power source, typically electricity from the grid, supplies the necessary voltage and current to the welding machine.
Electrode: The electrode is a conductive material that carries the electrical current to the workpiece, creating an arc.
Arc: An electric arc is a controlled discharge of electricity across a gap between the electrode and the workpiece. This arc generates intense heat, melting the metals and forming a weld.
Welding Cable: The welding cable connects the power source to the electrode holder and the workpiece clamp.
2. Diverse Applications of Electric Welding Machines
Electric welding machines find applications in a wide range of industries and tasks:
Construction: In construction, welding machines are used for joining structural steel components, fabricating metal structures, and repairing equipment on job sites.
Manufacturing: Welding plays a pivotal role in manufacturing, contributing to the production of everything from automobiles to appliances.
Aerospace: Precision welding is critical in the aerospace industry for creating aircraft components that demand both strength and lightweight design.
Shipbuilding: Welding machines are indispensable in shipbuilding, as they enable the assembly of massive steel hulls and intricate metal systems.
Automotive: Automotive manufacturing relies on electric welding machines for assembling car frames and other components.
Artistic Welding: Some artisans and craftsmen use welding machines to create intricate metal sculptures and decorative pieces.
3. Safety Considerations
Safety is paramount when working with electric welding machines. Here are essential safety measures to follow:
Protective Gear: Welders must wear proper protective gear, including a welding helmet with a darkened visor, flame-resistant clothing, welding gloves, and safety boots.
Ventilation: Work in well-ventilated areas or use exhaust fans to remove fumes and gases produced during welding, as they can be harmful if inhaled.
Eye Protection: Protect your eyes from harmful UV and IR radiation by wearing a welding helmet with an appropriate shade level for the welding process.
Electrical Safety: Ensure the welding machine is grounded correctly, and inspect cables for damage before use. Avoid wet or damp conditions when operating the machine.
Fire Safety: Have fire extinguishers readily available, as sparks and molten metal can pose a fire hazard. Keep flammable materials away from the welding area.
4. Maintenance and Care
To prolong the life of an electric welding machine and ensure its continued reliability, regular maintenance is crucial. Key maintenance tasks include:
Cleaning: Keep the machine and its components clean, removing dust and debris that can affect performance.
Inspection: Regularly inspect cables, connectors, and the electrode holder for signs of wear or damage, and replace any faulty parts promptly.
Cooling System: Ensure the cooling system, if applicable, is functioning correctly, as overheating can damage the machine.
Electrode Selection: Use the appropriate electrode for the type of welding being performed, as different electrodes are designed for specific materials and applications.
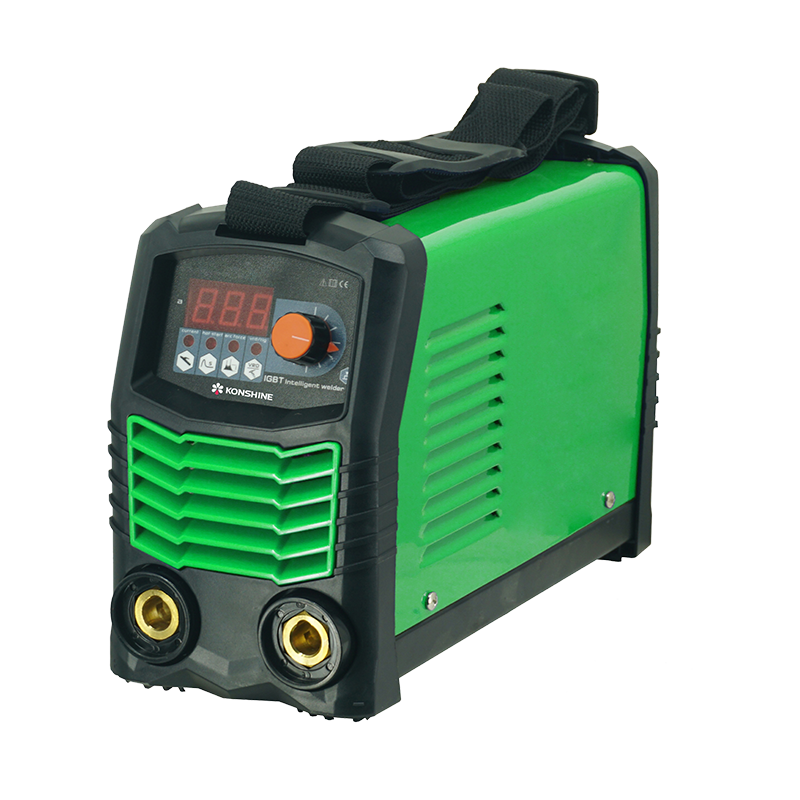